Delving into the world of DIY printing, you may find starting screen printing an appealing endeavor. However, a lingering question may be: what do I need to start? This guide will not only elaborate on the ten vital tools required to initiate your screen printing journey, but will also weigh the pros and cons of a DIY approach against using an established print shop.
1. Screen and Frame
Above all, a screen and frame assembly is the cornerstone of your screen printing setup. The screen consists of a fine mesh stretched over a robust frame. The frame is typically made of wood or aluminum, both materials offering their unique advantages. Wood is cost-effective and offers a vintage appeal but might warp over time. Aluminum, on the other hand, is durable and warp-resistant, ensuring a long-lasting performance. The mesh can be synthetic or metallic. The choice depends on your budget, durability needs, and the detail level in your design. When starting screen printing, a high-quality screen and frame are crucial to your success.
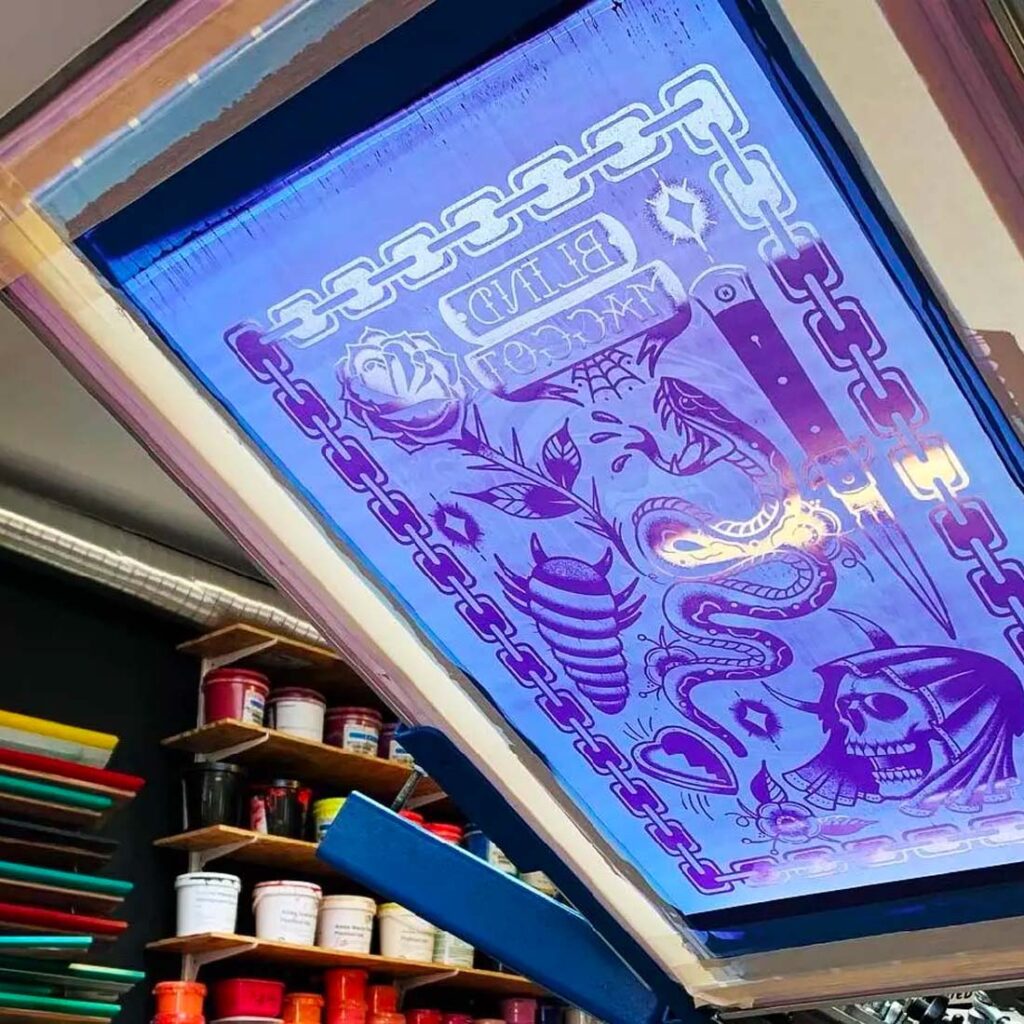
2. Photo Emulsion Kit
This kit comprises the emulsion, sensitizer, and remover. The emulsion is a light-reactive substance that you coat your screen with to create your design stencil. The sensitizer activates the emulsion, and the remover is used for cleaning the screen for reuse. Proper usage and storage of these components can significantly influence the quality and durability of your prints.
3. UV Light Source
This tool is used to expose your design onto the emulsion-coated screen. A UV light source can range from a simple 500-watt work light for beginners to a commercial exposure unit for professional settings. Your choice will depend on your budget and the volume and precision of prints required.
4. Transparency Film
Notably, a transparency film serves as the carrier of your design. You print your design onto this film, which then gets exposed onto the screen. Opt for a high-quality film to ensure your designs transfer accurately onto the screen.
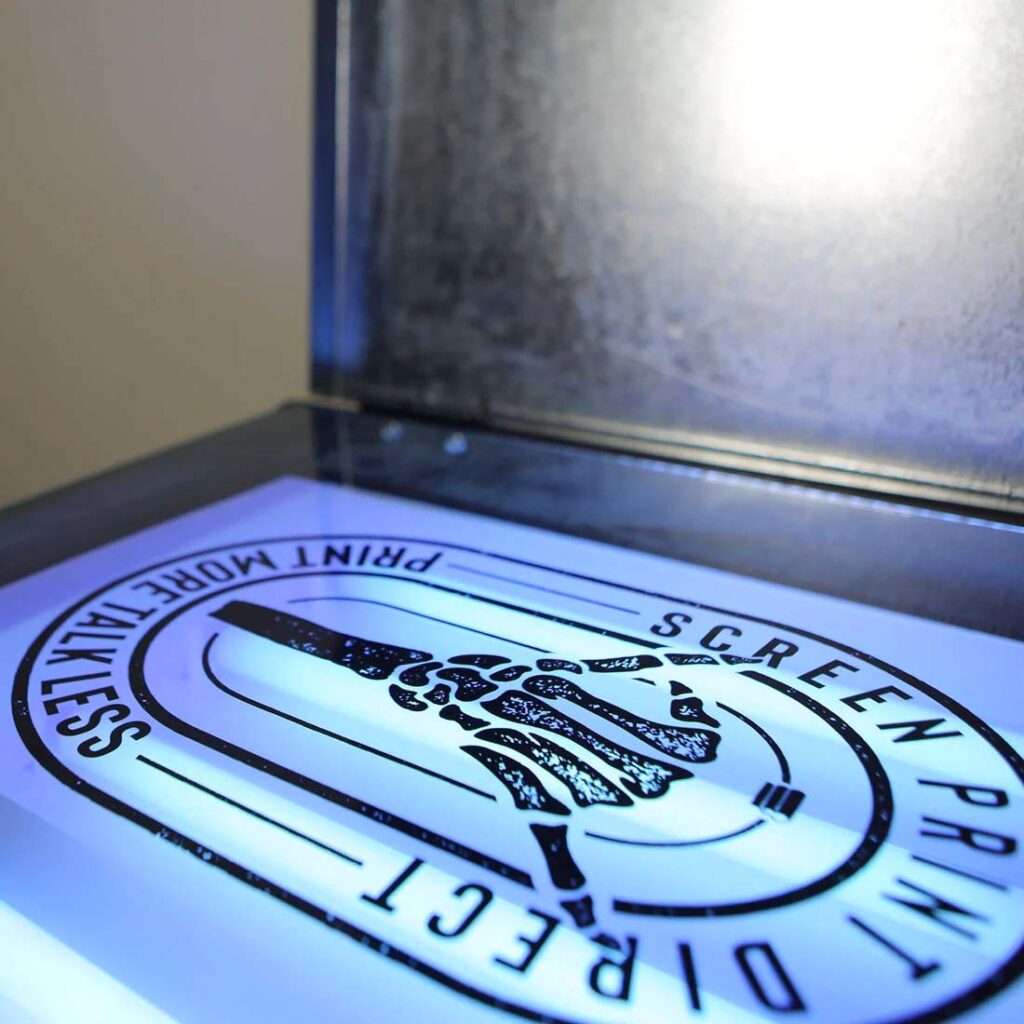
5. Screen Printing Inks
Screen printing inks bring color and vibrancy to your designs. These inks are specially formulated to adhere to various materials, including fabric and paper, and they come in a multitude of colors. Quality inks can ensure your prints remain vibrant and durable over time.
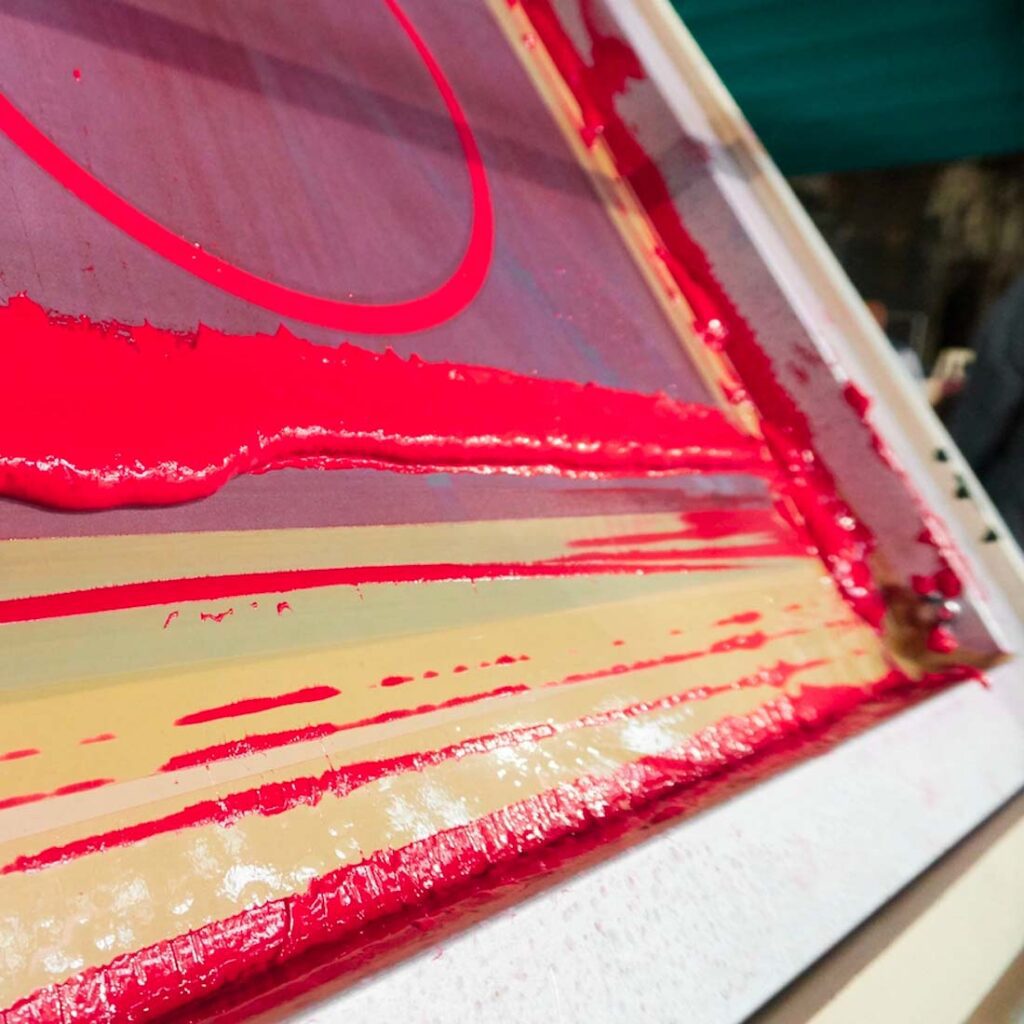
6. Squeegee
A squeegee is a rubber blade attached to a wooden or metal handle. It is used to evenly push the ink through the screen onto the printing surface. Squeegees vary in size and hardness, and your choice depends on the size of your design and the level of detail required.
7. Screen Printing Press
This tool holds your screen and the substrate (the item you’re printing on) in place. This can range from a simple one-color press to complex multi-color, multi-station presses. Investing in a quality press can enhance the precision and consistency of your prints.
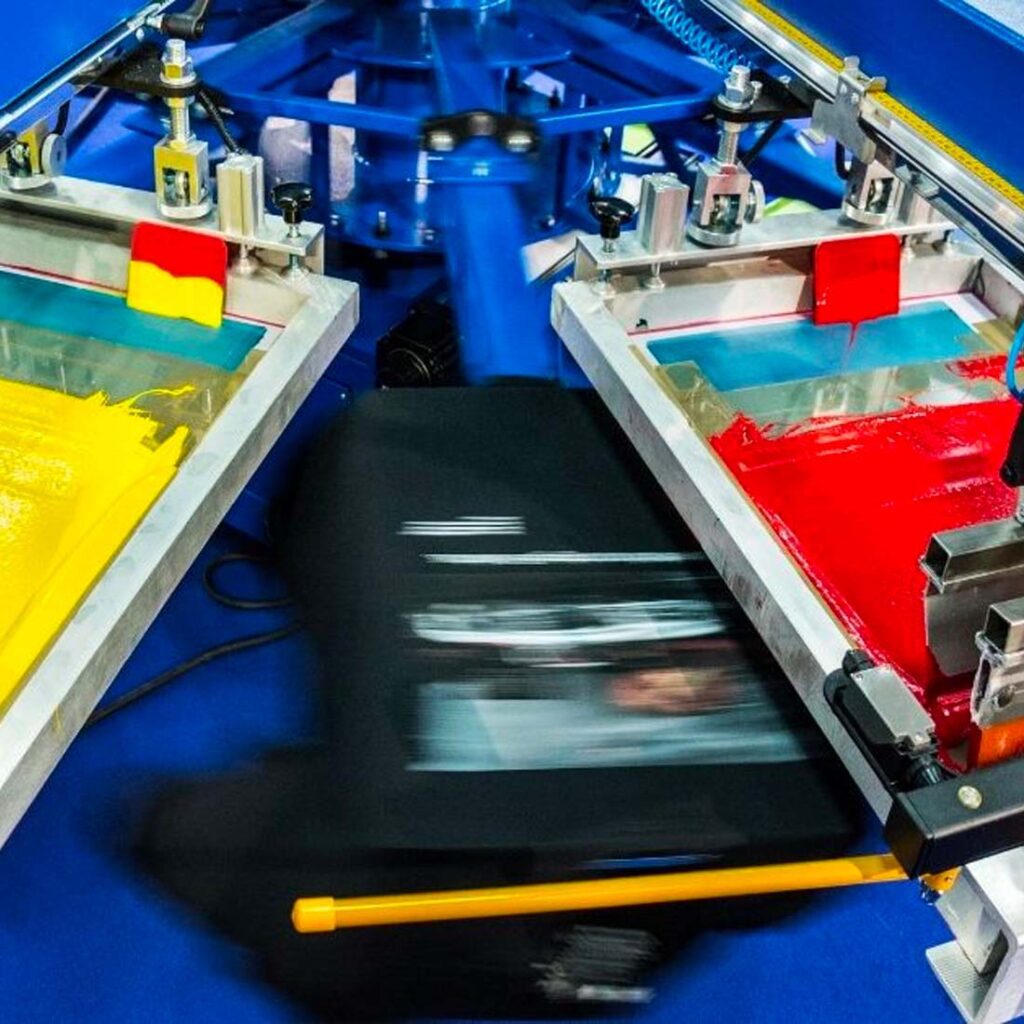
8. Printing Surface or Pallet
This is a flat surface where you place your substrate for printing. It can be coated to prevent ink absorption, thereby ensuring a smooth printing process and a high-quality end product.
9. Screen Printing Software
Software like Adobe Illustrator or Photoshop allows you to create, adjust, and perfect your designs before printing. Opt for a user-friendly, feature-rich program that can support your design needs.
10. Cleaning Supplies
Lastly, maintaining your screen printing tools is crucial for their longevity and performance. Invest in a good press wash for cleaning screens, an emulsion remover for reclaiming screens, and a scrub brush and power washer for effective cleaning.
DIY vs. Established Print Shop
Starting screen printing from scratch can be rewarding, offering a sense of fulfillment and the freedom to express creativity. However, it also requires a significant investment in time, money, and effort to acquire the skills, tools, and workspace necessary.
On the other hand, leveraging the services of an established print shop comes with its own advantages. Experienced professionals at print shops handle your work and assure high-quality, consistent results. They equip these shops with advanced tools and machinery, enabling a wide range of print options, the capacity for large volume orders, and swift turnaround times.
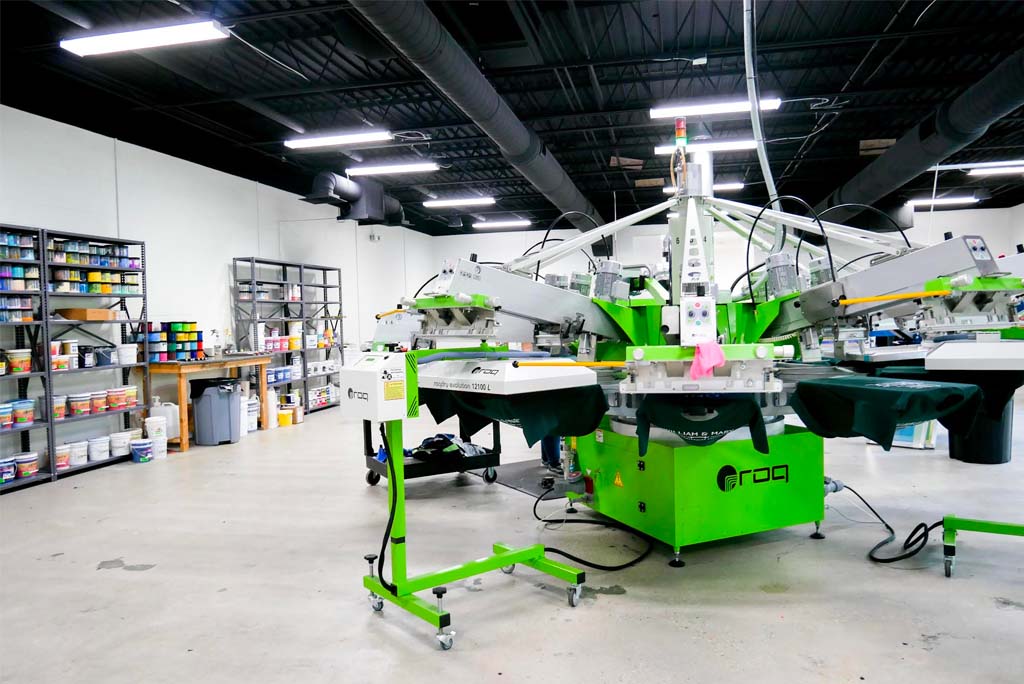
In addition, print shops can offer valuable advice on design, materials, and techniques, making your printing project easier and more successful. This could be a beneficial route if you’re looking for professional results without the steep learning curve or the initial investment of setting up your own screen printing operation.
In conclusion, whether you decide to venture into screen printing as a DIY project or choose to work with a professional print shop, the key lies in understanding your needs, budget, and expectations. It’s all about finding the balance between your creative aspirations and practical considerations.