Introduction
T-shirts. We all have them, we all wear them, but have you ever considered the creative process that transpires behind the scenes to create the captivating designs that embellish these common garments? It’s a process that is as intricate as it is fascinating – screen printing. This method, with its deep historical roots, has evolved over the centuries into a sophisticated technique.
Screen printing, or silk screening, is a time-honored printing method that has journeyed through time, from its earliest inception in ancient China to its modern-day applications across a myriad of industries. Its versatility and adaptability have cemented its place in the textile industry, with t-shirt printing being one of its most popular uses. This comprehensive guide delves into the captivating world of screen printing, demystifying its processes, highlighting its advantages, and showcasing why it remains the dominant technique for t-shirt design worldwide.
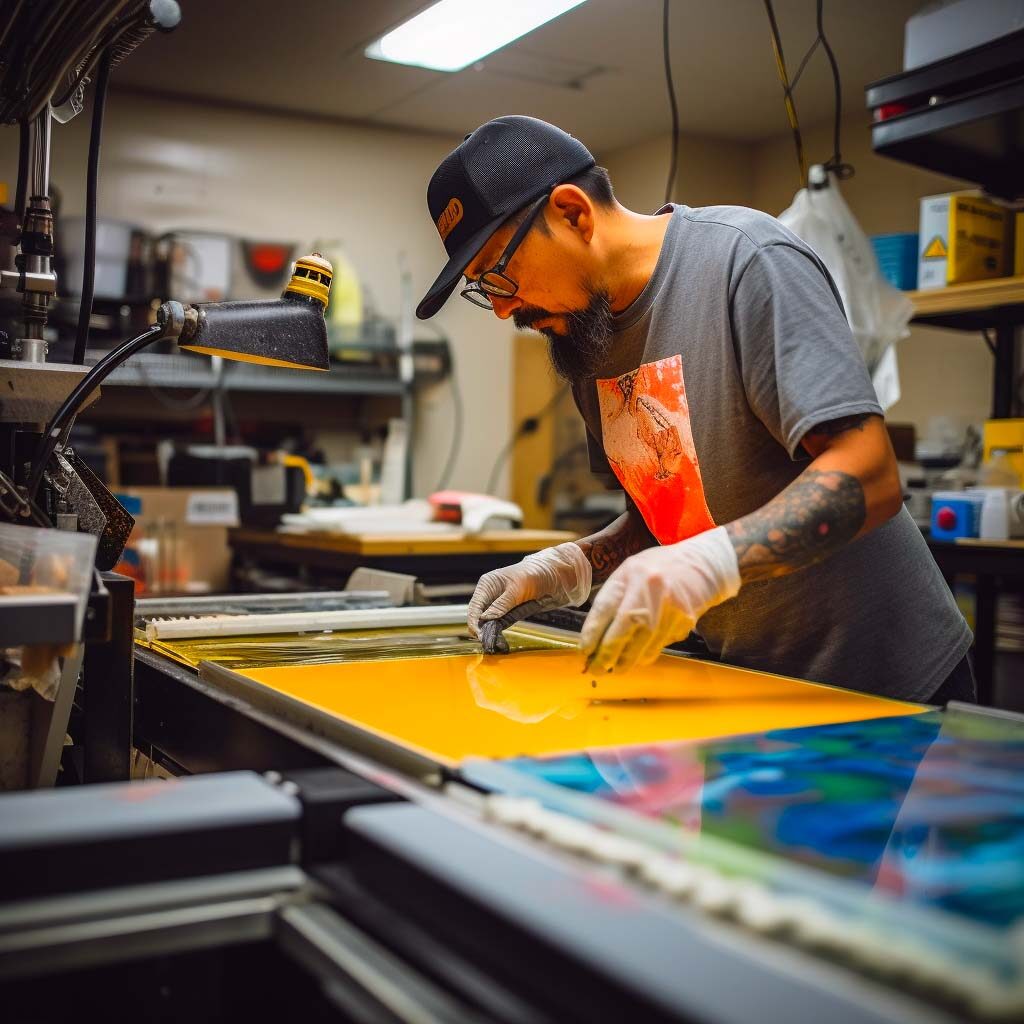
What is Screen Printing?
In the world of apparel, screen printing has held its place as the preferred method for t-shirt designs. This is primarily due to its ability to produce vibrant, long-lasting colors and its cost-effectiveness for large runs. It’s the reason why many of your favorite t-shirts, even after countless washes, still hold their dynamic designs and colors.
The Materials Involved
The core materials involved in screen printing are the screen, the stencil, the squeegee, and the ink. Modern screens are typically made from polyester, a synthetic material that can withstand the rigors of the printing process. They come in different mesh counts, which determine how much ink is deposited onto the surface. A lower mesh count allows more ink to pass through. A higher mesh count provides more detail but with less ink.
The stencil, which is applied directly to the mesh screen, is made from a photosensitive emulsion. This emulsion is coated onto the screen and then exposed to light. The areas of the screen covered by the design block the light, while the rest of the emulsion hardens. The unexposed areas are then washed away, creating a precise stencil of the design.
Squeegees are an essential tool in screen printing. They are used to evenly push the ink through the mesh screen and onto the surface. The squeegee’s hardness, or durometer, can be adjusted depending on the level of detail and the type of ink used.
The ink used in screen printing is specially formulated to be thick and vibrant, ensuring a high-quality print that can stand up to washing and wearing.
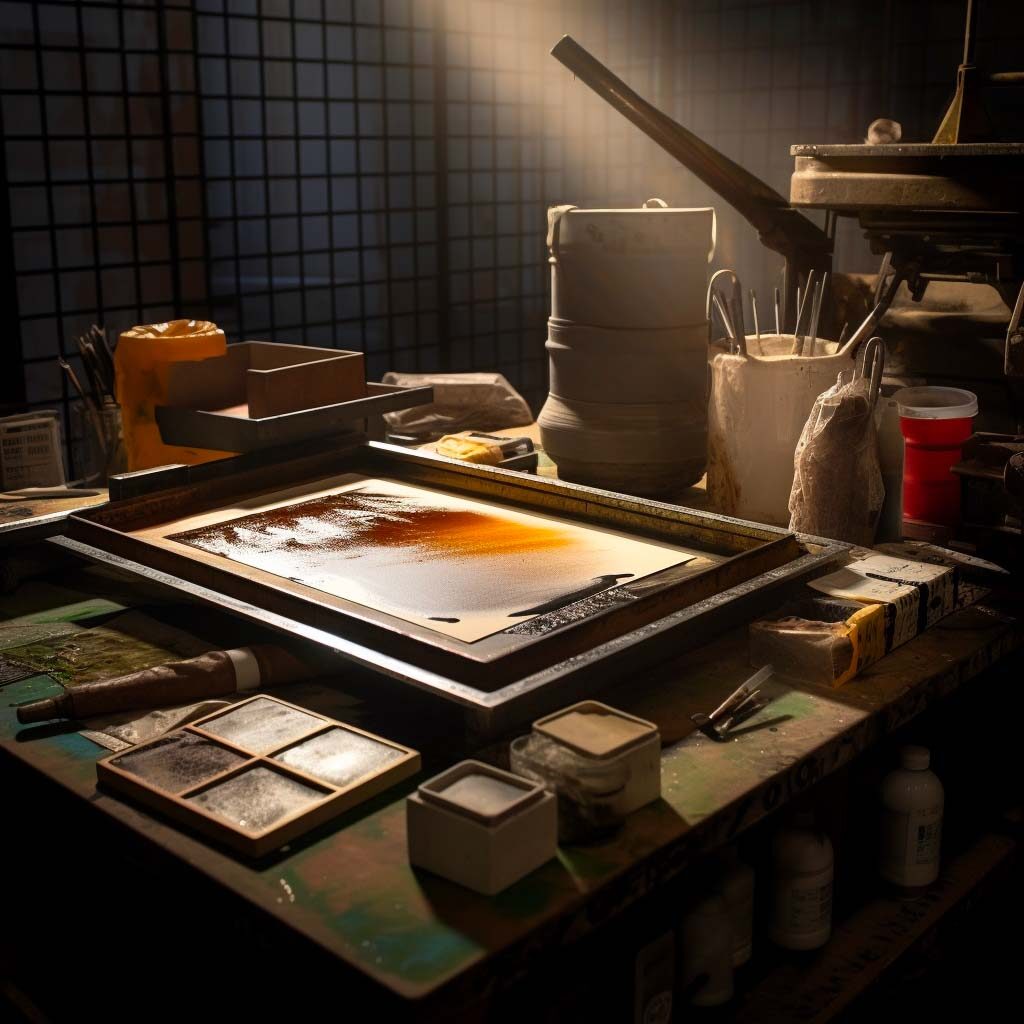
Durability and Longevity
There’s a reason why screen printing has stood the test of time. The process creates a print that can withstand the rigors of daily wear and repeated washing. Unlike other print methods, the thick inks used in screen printing soak into the fabric, creating a bond with the fibers that can last for years.
It’s this durability that makes screen printing the preferred choice for garments that need to last, like band merchandise, sports jerseys, or work uniforms. While other printing methods may fade, crack, or peel over time, a screen-printed design will retain its vibrancy and structure for years to come.
Cost-Effectiveness for Large Orders
While setting up for a screen print run can be laborious, once the screens are prepared, printing can be done quickly and efficiently. This makes screen printing an economically wise choice for large orders.
Because each color in a design requires a separate screen, screen printing can seem costly for small runs. However, once the screens are made, they can be used over and over again, bringing the cost per unit down significantly for larger orders. This scalability is what makes screen printing the go-to method for businesses needing large quantities of custom apparel.
Rich, Vibrant Colors
The vibrancy and depth of color achievable with screen printing are hard to match. The thick inks used in the process don’t just sit on top of the fabric – they soak into and bond with the fibers, resulting in colors that truly pop.
Screen printing also allows for custom color mixing. Unlike digital printing methods that use standard CMYK inks, screen printing inks can be mixed to create any shade or hue imaginable. This opens up a world of possibilities for your designs, and it’s one of the many reasons why artists and designers love screen printing.
Design Creation
The journey of a screen-printed t-shirt starts with a design. This design is typically created digitally, using design software like Adobe Illustrator or Photoshop. The design must be broken down into individual colors because each color will be printed separately.
The design is then printed onto transparent acetate films to create what’s known as a film positive. This film positive acts as a sort of stencil for the design, with the opaque areas blocking out light during the screen exposure process.
Screen Preparation
The next step is preparing the screens. Each screen is coated with a photosensitive emulsion, a substance that hardens when exposed to light. The film positive is placed on top of the coated screen, and the whole thing is exposed to bright light.
The light hardens the emulsion that isn’t covered by the design on the film positive. After exposure, the unhardened emulsion is washed away, leaving a precise stencil of the design on the screen. This screen is now ready for printing.
Printing the Design
With the screen prepared, it’s time for the fun part: printing. The screen is placed onto a press, with the t-shirt beneath it. Ink is added to the top of the screen, and a squeegee is used to pull the ink across the screen, pressing it through the stencil and onto the t-shirt.
Each color in the design is printed one at a time, using a separate screen for each color. This can be a time-consuming process, especially for designs with multiple colors, but the result is a vibrant, multicolored print that’s worth the effort.
Curing the Ink
Once the design has been printed onto the t-shirt, it needs to be cured. Curing is the process of drying the ink so that it sets into the fabric and won’t wash out. This is typically done using a conveyor dryer, which subjects the t-shirts to a precise amount of heat for a specific amount of time.
Curing is a critical step in the screen printing process. If the ink isn’t properly cured, it can wash out or fade prematurely. But when done correctly, it ensures a durable, long-lasting print.
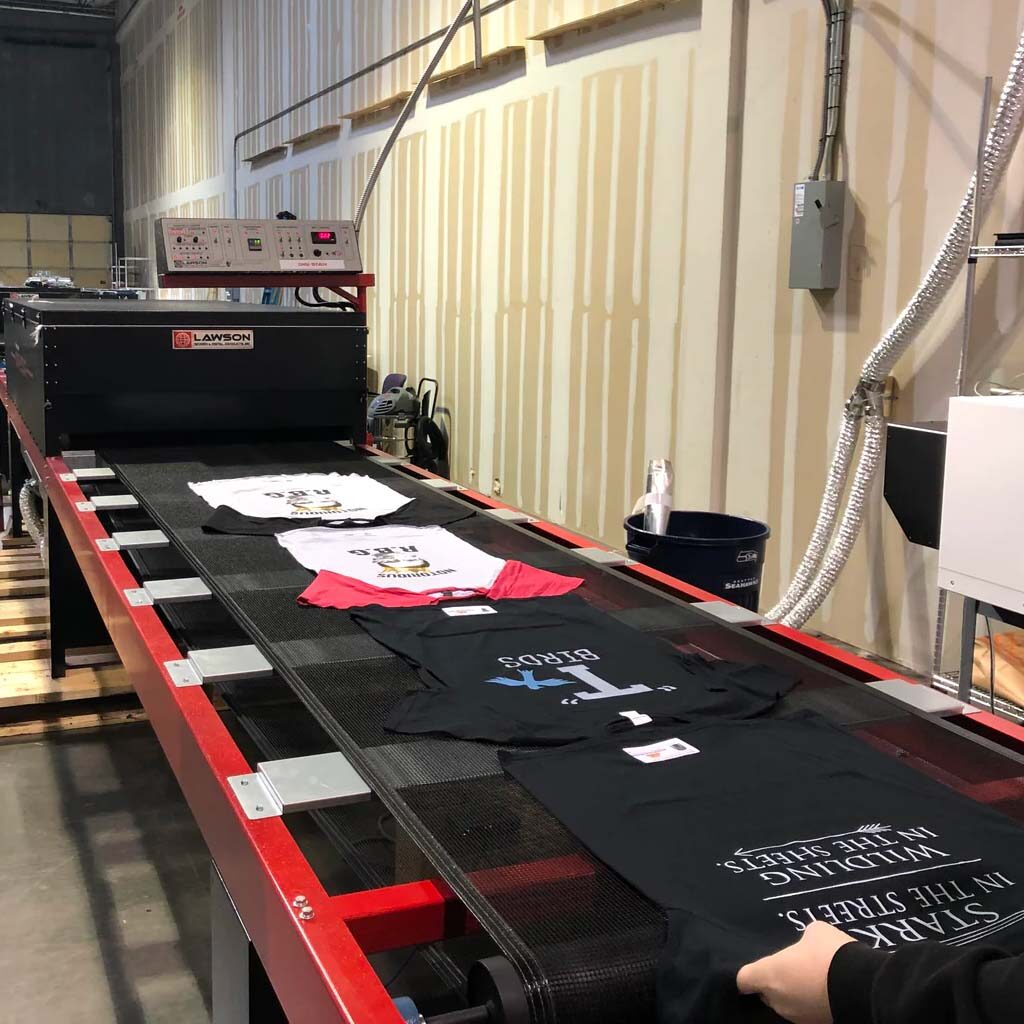
Conclusion
Screen printing is a beautiful blend of art, science, and craftsmanship. It requires a mix of technical knowledge, practical skill, and artistic creativity. The result is a high-quality, durable, and vibrant design that can last for years. Whether you’re an artist wanting to share your designs with the world, a business owner in need of promotional apparel, or just someone who appreciates a well-made t-shirt, understanding the screen printing process can give you a newfound appreciation for this ubiquitous garment.